Streamlining the process of
Bunk Bed Customizations
A professional project undertaken at Boingg! in July 2022 to reduce financial losses, material wastage and standardize the production process of customised furniture. As the project lead, I followed a user-centred design methodology to study internal and external factors influencing the same. By conducting research on user requirements and studying the internal production process in detail, a simple, cost-effective solution was developed that aligned both user and business needs. The solution, a Typeform, helped to limit user choices thereby enabling the production team to follow the standard production process which resulted in a reduced error rate.
This project gave me an insight into the restrictions on the scalability of certain ideas.
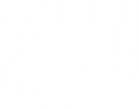
Problem addressed
Uncontrolled customisation of bunk beds, leading to errors in production and changes in design language of the brand.
Stakeholders
-
Customers
-
In-house designers
-
Production team
-
Sales team

Research & Analysis
Exploring various research methods to gain insights into the production & sales process, and consumer needs.
Conducting interviews and observations with the production team to identify pain points.
Analyzing standard vs customized sales to optimize time and revenue.
Interviewing sales teams to enhance understanding of customer needs.
Aligning research findings with business objectives for strategic growth, a standard Typeform was designed which offered the following customisation options
Customization Options Offered
Size
Top bunk size remains the same throughout (6ft x 3ft)
​
Bottom bunk size options range from 6ft x 3ft to 6ft x 6ft
Colour
3 bestsellers + colours available from vendor throughout the year
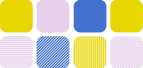
8 bestseller prints across gender and age groups in combination with finalised colours
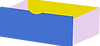
Storage
4 storage options based on most chosen by customers and production efficiency

Climbing
3 climbing options in accordance with available space and cost of the asset
The Typeform that was designed:
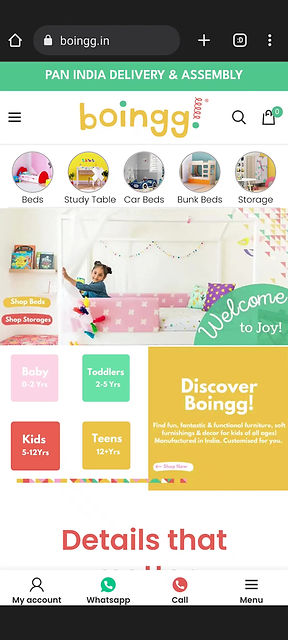
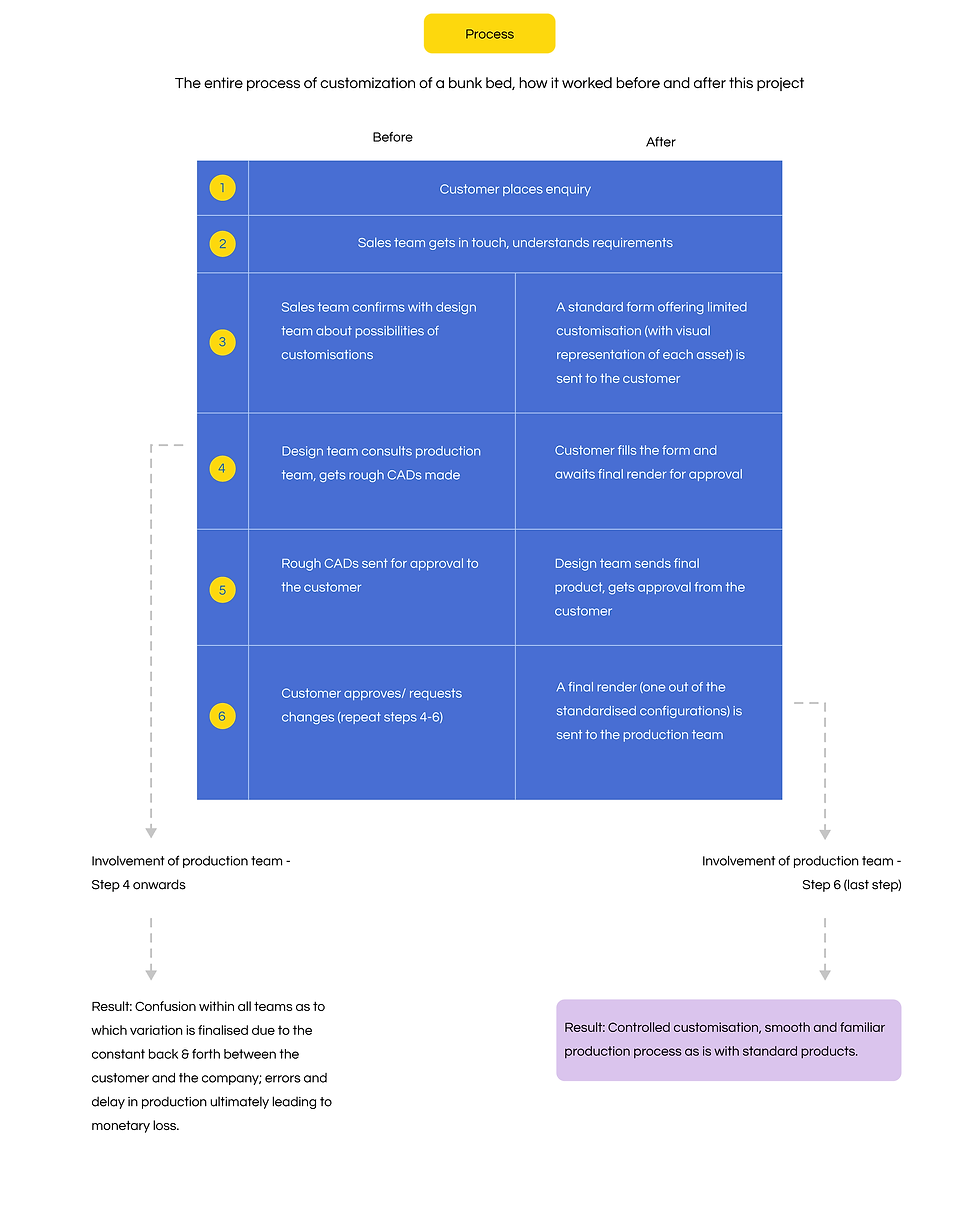